1) Loose your weight
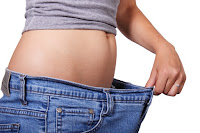
In a usual weight loss program, we loose our weight and then gain it once we stop the program. But in a good lean enterprise, you focus at it often. Remember, this does not mean firing the people or doing a massive re-org. These are the best treatments that last a month!
Loosing weight in Lean, implies to keep looking at ways to continuously shed away what we would collect as we grow and do new stuff. Those could be excess inventory, unused or rarely required tools, expensive services (getting more expensive day by day), unproductive events, inflated processes, never ending projects, etc.
2) Wash yourself
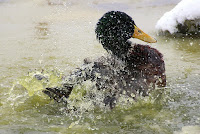
Cleanliness is both the abstract state of being clean and free from dirt, and the process of achieving and maintaining that state. Keeping surrounding clean, allows to identify dirt and dirt making elements, helps loose your weight sooner. Cleanliness improves productivity, drives discipline, promotes transparency, limits back side gossips. The best part of it is we get encouraged to be clear in thoughts, words and deeds.
Daily Kaizen, Kaizen events and focus on 5S(sort, set, shine, standarize and sustain) helps the teams to keep the surroundings and environment clean.
3) Learn to say Sorry and Thanks more often.
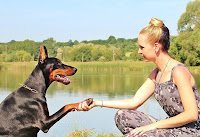
Every team member in your team is leader in himself/herself. And in such a diverse teams, the biggest impediment in front of the team is leadership style of everyone. One action is perceived by different people differently based on their beliefs, egos and attitudes. Interpersonal strife and collaborative challenges rule until open communications and reiteration of meanings serve as the key.
Humble confidence is necessary while dealing with people and leading them. Accepting the mistakes and moving on becomes the guiding factor. Learning from ones/other's mistakes builds upon the experience and showing gratitude adds the flavor of humbleness.
Encourage Gemba walks, Gembutsu, Genjitsu and Genri and Genichi styles at the workplace.
4) Stitch in time, Save nine!
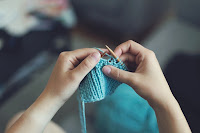
Lean is all about learning and improving. Learning from failures is the key. The failure is not an event. It is the result of a chain reaction. We need to identify the root cause (and not the root person) for the event and stitch over there. This stitch on time, saves further chain reaction.
Identify that small gap in your system which made the person fail!
5) What goes around, comes around!
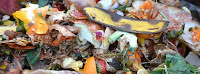
Every business produces waste. Lean promotes reducing the waste. The waste could be unused inventory, WIP items pending too long, approval chains, scrap and many more. The businesses are meant to produce profit, value and brand.
When we start reducing the waste, productivity increases. This results in increased profit and value. This creates stronger brand recognition. All this is done to provide satisfaction to the customer. If we produce more waste, then customer will get lesser value and the result is "dis-satisfied customer".
So if you produce more waste, then more waste will come back to you. If you produce more value, then more value will come back to you in terms of profit.
6) Meditate
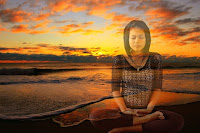
Yes, you heard it right! With the hectic pace and demands of modern life, many people feel stressed and over-worked. There are many things in life that are beyond our control. However, it is possible to take responsibility for our own states of mind – and to change them for the better. Meditation practices are techniques that encourage and develop concentration, clarity, stability, satisfaction and a calm seeing of the true nature of things.
When you see the true nature of the things going on in your enterprise/project, you start recording them. Once those are recorded, those get improved. Periodic audits identify gaps those are wastes, The process improvement reduces wastes. All improvement opportunities drive towards consistency, predictability, stability, and team satisfaction.
Note: The headings given to each of the above paragraphs, are not to be meant for taken literally; take those as a pun.
This comment has been removed by the author.
ReplyDeleteThis comment has been removed by the author.
ReplyDelete